Construction of iron frame warehouse for agriculture
The iron frame warehouse for agriculture is transferred with DIY.
There was information of disposing of the light iron frame warehouse for agriculture because my acquaintance planned to build new house. Then, I decided to get this and to transfer it to my country. I took in DIY for years, dismantled the iron frame warehouse, transported, and constructed it.
Dismantlement, transportation of warehouse, and assembly
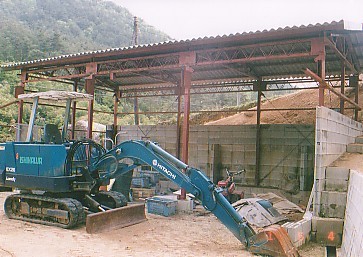
This is a photograph where the light iron frame warehouse for agriculture is assembled in May, 2001. First of all, the place where the warehouse is built is secured. The width is about 8m, and there is about 6m depth. It takes about two years to assemble it here.
Because the north and the west are slopes of about 2-5m in height and the construction place cannot be secured enough, the warehouse decided to be put into half (about the maximum 2m) the state buried under the soil and to be built though is the west of the main building place.
The wall in the part that had been buried under the soil built the grain silo made of the concrete block on the corner of the northwest of the warehouse. The storing can of rice decided to be put here and to store the brown rice.
Moreover, it dug up the pit of about 120cm in depth in the below the floor level of the warehouse, it enclosed with the concrete block, and it made it to pit type storehouses of the potatoes. Water doesn't come out from this place originally in the place in the mountain that is the ridge even if a little digging up the underground because moisture is a little.
The height of the base is originally assumed to be about 40cm for the entrance low, and moisture prevention and this warehouse has raised the umbrella to as many as 2 pieces in the block though as many as one piece (about 20cm in height) in the block was used for the base.
The backhoe was used for the assembly of the iron frame. Because the iron frame is heavy, it is not at all assembled in human strength. The slate roof is put when the iron frame unites and it goes up. Even if it has already rained, it is safe if coming here.
This iron frame warehouse already seemed to have passed from construction about 25 years when having inherited it. The rustproof (rust stop) painting of oily is done though there is no iron frame when it rusts too much. Especially, it paints at once when welding in the welding part.
The gutter is put in surroundings of the warehouse.
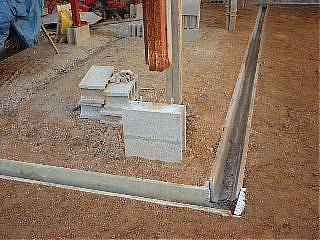
The gutter of about 150mm in width is put in surroundings of the warehouse because of drain. It is possible to work alone if this uses the backhoe.
The outside and a slope side of the building also cover with concrete. Rainy water is made to ground, not seen, and led to the gutter. There is little thing of which moisture comes in the warehouse if it does so.
The pillar in this photograph has been hardened with the concrete between bases because it is short.
Making the floor for the second floor
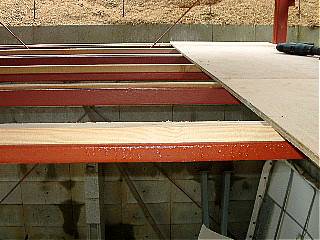
It decided to make it to two stories making the floor for the second floor of about 2m in height in the part of about 2/3 of the floor space of the first floor to increase the amount of storage though this warehouse was originally an one-storied house.
Because a part of the wall had been made made of the concrete block, a remaining iron frame decided to be used to reinforce the floor. It reinforces it to the part that supports this iron frame with another iron frame. The iron frame was installed by the electric welding.
The tree is put in the iron frame because the size of the iron frame is uneven and the height of the floor is adjusted.
The concrete panel with a low price was used for the second floor.
Put the outside slate wall
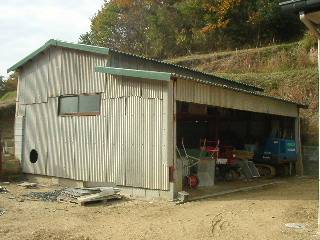
The window had been installed before the slate of the outside wall was pasted. Because the lighting is few and dark in the window that is originally, the area of the window of the west and the north has been increased. Moreover, it puts directly from the ground on the outside in the second floor of the north side and the beginning entrance is installed.
So as not to see it from the outside in the window of the transparency, the spray paints were sprayed from the inside on the pane.
A big hole with a round southwest is an exhaust vent for the grain dryer. When not using it, closes it.
The floor is hardened with concrete.
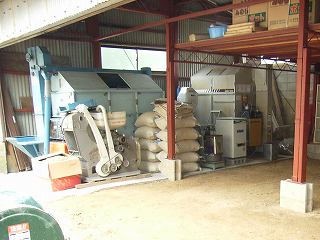
To prevent the soil from going up in doing that prevents moisture from the floor and the warehouse, the floor of the first floor is hardened with concrete. It mixes concrete mixing sand, cement, macadam, and water with an electric cement mixer.
It is assumed that there only have to be 5cm or more though a concrete thickness wants about 10cm. This photograph is the one when the area of about 1/3 is hardened with concrete.
It digs up the hole of about 1.3m in depth on the floor because the root cellar is made on the floor on the north side.
Installation of the shutter, painting of the roof and the wall, and electrical work
Three shutters are installed on all aspects as an entrance of the east side at the end. The rail of an old shutter (pillar of the shutter) was not able to be used ..umbrella.. raising the base by about 20cm because it was short. The new one was ordered and installed.
The roof and the wall were painted in paints for the slate several times. Because the slate was deteriorated if it did not paint ahead of time, the roof was painted at once for the time being. Afterwards, the slate roof was washed with the high-pressure washing machine and painted. Because the wall doesn't have suddenness, it paints only in the painting of part sooner or later.
Electrical work wires for the single phase 100V and single phase 200V for the farm machinery. The single phase 200V is for the inverter and for the welding machine converted into the three-phase circuit 200V used with the huller.